In 2021, over 400,000 workplace injuries were caused by exposure to harmful chemicals. This figure reminds us how important it is to manage chemicals properly in commercial settings.
One way businesses have been curbing the number of workplace injuries from chemical exposure is to adopt a chemical management system.
Chemical management systems are meticulously designed to facilitate the efficient and safe handling, storage, dispensing, and tracking cleaning chemicals and related products. This approach ensures responsible and effective chemical management, a cornerstone for workplace safety.
Let’s look closer at chemical management systems and how they can help improve workplace safety.
What is a Chemical Management System?
A chemical management system is an arrangement of tools and protocols for handling and controlling various aspects of chemical usage within a commercial setting.
This system encompasses a range of features, with components like automated dilution control and real-time chemical level tracking.
Automated dilution control is a pivotal aspect of a chemical management system. By automating the dilution process, the system minimizes the margin of error, ensuring that the intended chemical concentrations are maintained consistently.
The main objective of a chemical management system is to increase productivity and improve workplace safety standards.
3 Components of a Chemical Management System
Here are three components of a chemical management system that come together to increase productivity and improve workplace safety standards.
- Accurate Chemical Dilution
- Chemical Labeling
- Chemical Inventory Management
Let’s examine closely how each component contributes to a safer and more productive work environment.
1. Accurate Chemical Dilution
A central aspect of a chemical management system is an automated dilution control system to reduce the risks associated with chemical exposure and the use of over or under diluted solutions.
2. Chemical Labeling
The use of color-coded chemical labeling is a hallmark of many chemical management systems.
This visual aid surpasses language barriers, simplifying chemical identification even for staff with minimal training. The primary goal is to diminish the likelihood of an employee accidentally using the wrong chemical for a given cleaning task.
3. Chemical Inventory Management
Another defining feature of a solid chemical management system is how it enables real-time tracking of chemical inventories.
Pro Tip: Tracking chemical inventories in real-time is primarily a component of chemical management systems in the laundry and warewash industries.
This feature ensures that janitorial staff remain well-informed about current stock levels, preventing the chance of a surprise shortage during crucial cleaning operations. The result is a more effective workflow, with minimized disruptions and safety risks.
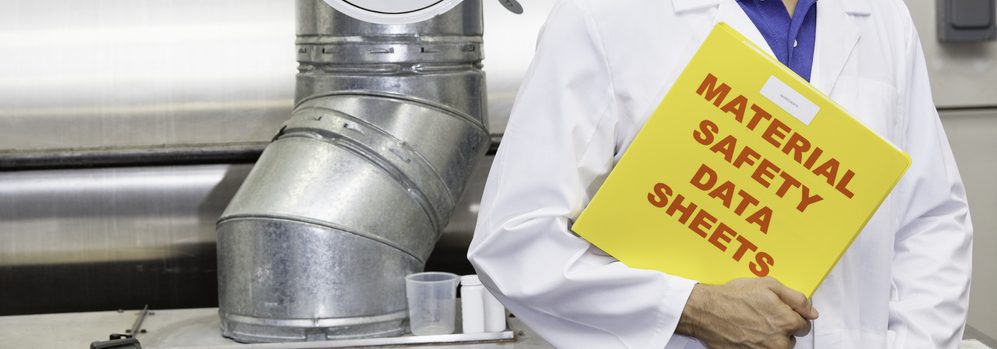
4 Safety Benefits of a Chemical Management System
Chemical management systems are all about streamlining processes to improve workplace safety.
To underscore this point, here are four ways that a chemical management system improves workplace safety:
- Reduces the Risk of Chemical Exposure
- Reduces the Risk of Using Solutions That are Over or Under Diluted
- Minimizes the Risk of Using the Wrong Chemical
- Prevents Unexpected Shortages or Stockouts
Let’s break each of these down.
1. Reduces the Risk of Chemical Exposure
Through a system of bottle racks, tubes, hoses, and a chemical dispenser, an automated dilution control system can dilute cleaning solutions to the correct concentration for the task at hand with complete accuracy. As a result, employees no longer have to worry about the hazards of handling concentrated cleaning products.
2. Reduces the Risk of Using Solutions That are Over or Under Diluted
Where manual mixing introduces the risk of improperly diluted chemical solutions, automation prevents such mistakes from being possible. Automated dilution control systems ensure that the exact right amount of chemical is introduced to the solution each time, removing any chance of an over or under-diluted chemical solution.
3. Minimizes the Risk of Using the Wrong Chemical
The strategic use of color-coded labels becomes a safeguard against unintentional misuse of chemicals. The probability of employees selecting an unsuitable chemical is significantly reduced, mitigating risks associated with ineffective cleaning, potential surface damage, and chemical exposure.
4. Prevents Unexpected Shortages or Stockouts
The proactive nature of inventory monitoring serves as an important tool for janitorial crews, enabling them to proactively reorder chemicals before depletion. Proper chemical inventory management not only eliminates the possibility of a shortage but ensures a continuous and uninterrupted supply of essential chemicals. This reduces the risk of compromising safety due to the unavailability of critical cleaning solutions.
Final Thoughts
Accurate chemical dilution, chemical labeling, and chemical inventory management are all components of a chemical management system that combine to forge a safer working environment for your janitorial staff.
All three components collectively reduce the safety risks associated with chemical handling.
Whether you’re seeking to elevate workplace safety or establish a robust guide for chemical management, implementing a chemical management system is a proactive step towards these goals.
For further insights into the benefits of setting up a chemical management system at your facility, contact an Imperial Dade facility near you.
You can set up a free consultation with one of our Chemical Specialists, who will answer any remaining questions you have about dilution chemical management systems. They’ll even perform a free on-site or virtual evaluation of your facility, identifying areas for improvement in your current chemical management system.
Check Out These Related Articles and Videos:
- Dilution Control 101: Everything You Need to Know
- What is Dilution Control?
- How to Use a Dilution Control System in 4 Easy Steps
- Chemical Safety Tips For Reducing Insurance Costs & Workers’ Comp Claims
- The Importance of Proper Chemical Dilution
- Commercial Cleaning Coach – The Importance of Labeling Secondary Containers